Using innovation and creativity to deliver a state-of-the-art renewable fuel production plant
Market
Industrial Process
Key Services
Construction
Self-Perform
Delivery Method
Construction Manager at Risk (CMAR)Capacity
88MGY Ethanol ProducedWork Hours
700,000The challenge
Abengoa Bioenergy needed a greenfield ethanol plant that would implement Vogelbusch technology to produce 88 million gallons per year of ethanol and 230,000 tons of distillers’ grain solubles (DGS) per year. The project involved a tight schedule, innovative technologies, and the need to overcome engineering delays and equipment deliveries.
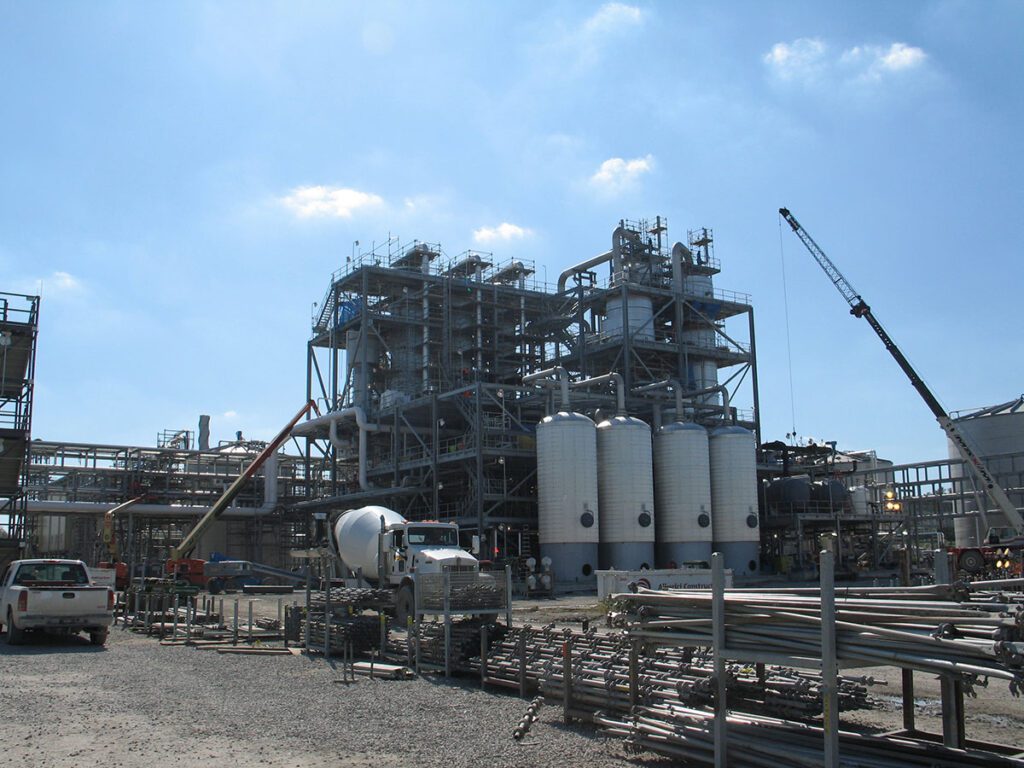
Key Facts
700,000 safe work hours
825,000 tons of corn consumed annually
Peak workforce: 650
Challenge met
As the construction manager, Alberici worked closely with Abengoa and the design team to provide preconstruction services, optimizing efficiency and cost-effectiveness. We self-performed over 700,000 craft hours, including concrete placement, structural steel erection, pre-engineered building erection, and process equipment installation. Alberici’s commitment to sustainability led to the use of new technologies like the Patent Logik360 radial concrete forming system and UltraCURE for concrete placement, reducing waste and labor costs while maintaining quality. When faced with engineering delays, Alberici implemented a six-day-per-week schedule with extended shifts, leading to an on-time project completion. Alberici decreased labor costs and improved quality by using UltraCURE during concrete placement instead of the traditional wetted burlap method. The net effect of these and other similar Alberici-led initiatives was a project delivered in a more environmentally responsible manner while significantly reducing project costs.