News & Insights
Dynamic Interdependencies: Constructing the North American EV Supply Chain

By Aaron Walsh, Market Leader, Automotive at Alberici
As automakers race to produce the next generation of electric vehicles, the EV supply chain is growing at a dramatic pace. Never have we seen this level of complexity in terms of concurrent design, procurement, fabrication and construction at this scale.
According to a 2022 report from Reuters, the world’s top automakers are planning to spend nearly $1.2 trillion through 2030 to develop and produce millions of electric vehicles (EV), along with the batteries and raw materials to support that production. These new investments are largely in North America and will establish a new supply chain linked by very large and novel facilities to source raw material and manufacture EV batteries.
There is ample opportunity for contractors to create value when design-building these novel manufacturing facilities. Partnering with the right collaborators is paramount. Trade partners must have the appetite, resources and competence to skillfully navigate dynamic interdependencies.
North American EV production is ramping up amid a host of constraints such as labor and equipment shortages, lack of advanced manufacturing experience and movement toward fast-track delivery to expedite speed-to-market. Historically, expertise in battery production has been centered in Asia, which adds language barriers to the list of challenges, as well as reconciliation of import and domestic standards. The convergence of the above factors allows construction managers and general contractors to facilitate on-time project delivery because of our position at the center of the project team.
People resources are the primary challenge and the industry’s top constraint, whether they represent skilled trades or construction professionals or designers. Below is a contextual roadmap based on experience for how we are overcoming challenges and helping clients build North America’s EV supply chain.
A new evolution: Advanced Manufacturing facilities
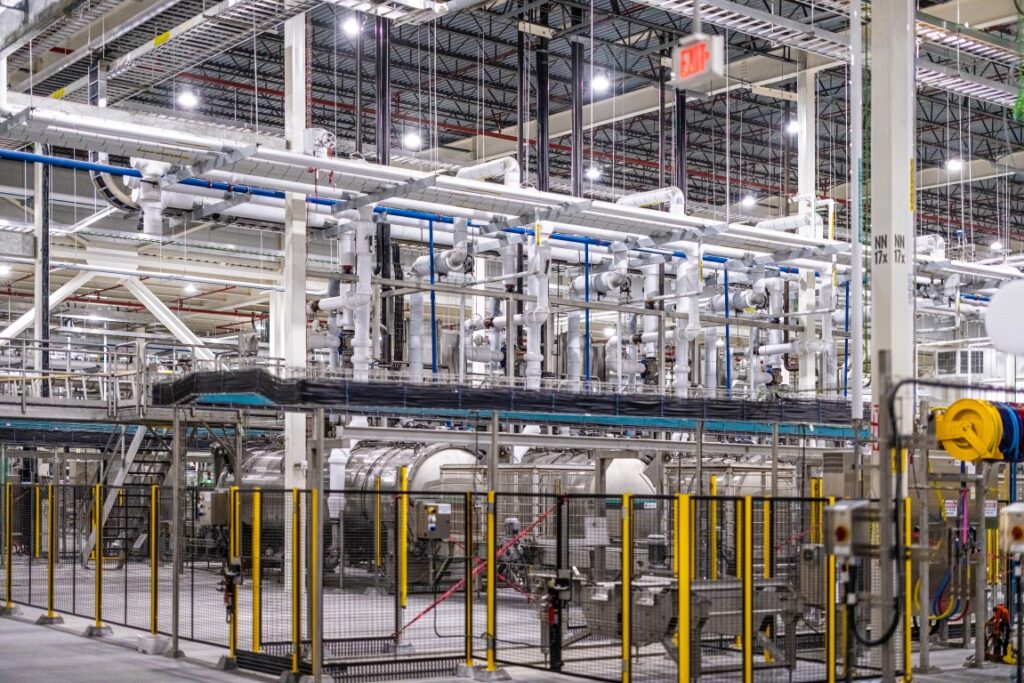
Advanced manufacturing facilities demand three to four times more mechanical and electrical equipment than traditional manufacturing facilities, and they use complex automation with sophisticated robotics.
In the U.S., federal incentives announced in 2022 are designed to lower the cost of electric vehicles and charging infrastructure while stimulating EV adoption. The U.S. alone aims to increase EV sales to 50 percent of all new auto sales by 2030.
The result for automakers is movement further into the advanced manufacturing space, long occupied by the pharmaceutical-, aerospace- and medical-manufacturing industries, where technology considerations are inextricably woven into each facility. They house massive “clean” and “dry” rooms with highly controlled air pressure and humidity, respectively. Material and equipment selection optimizes air ionization and uses grounding conductors to prevent static charges from damaging semiconductors. Building these advanced manufacturing facilities requires specialized trades in significant quantity, and experience is being developed at a rapid pace as projects are completed.
If you picture a Venn diagram, with traditional auto manufacturing on one side, and advanced manufacturing on the other, the overlap in the middle is currently widening with EV battery production kicking into high gear. More than $52 billion of North American EV manufacturing facilities have been announced since 2020.
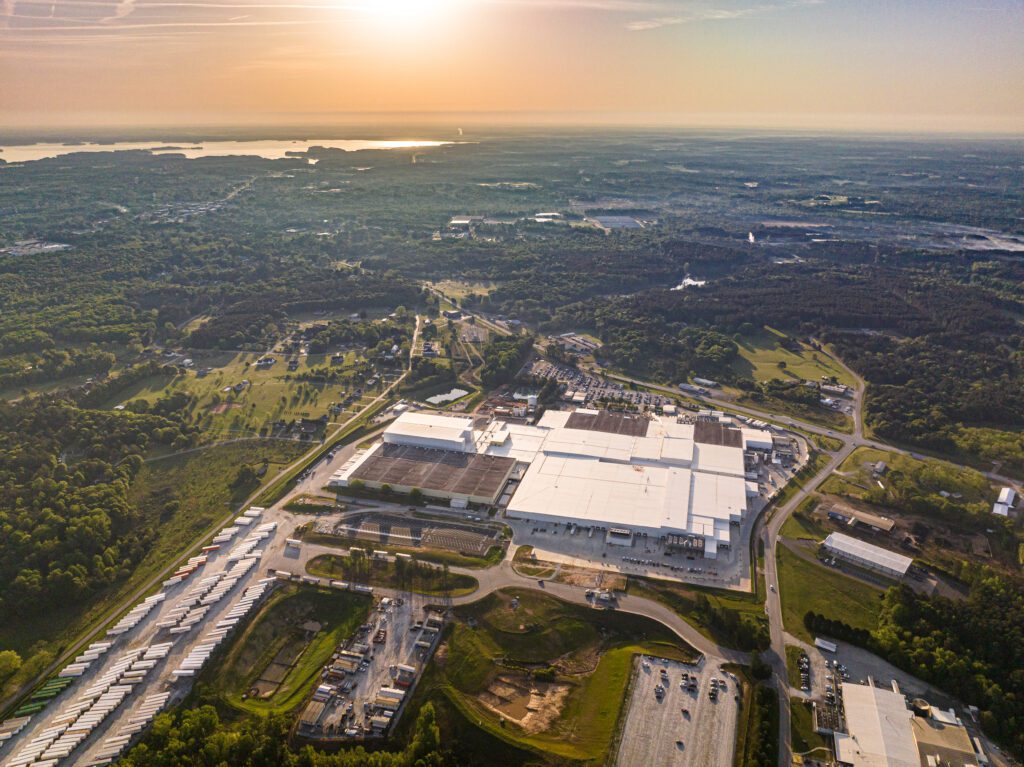
Massive in scope and imbued with technology, advanced manufacturing facilities use advanced mechanical and electrical infrastructure to create highly controlled environments.
‘Billion dollar landscape’
Historically, battery-manufacturing resources and expertise come from China, Japan and Korea. Raw materials, processed materials and finished lithium-ion batteries used in American cars are still predominantly sourced from Asia, but that will soon change and reduce the cost of battery manufacturing, making electric vehicles more affordable. Tax incentives correspond to percentages of battery components sourced, processed and assembled in North America.
If you look at a map of North America today, you will need to drop at least 33 pins to account for each of the multi-billion-dollar megaprojects underway to feed current and future EV production. Like energy production, its three-prong supply chain is comprised of upstream, midstream and downstream modalities. Each of the projects underway will result in a facility specifically built to support one of them.
These facilities have no direct analog in the automotive industry’s long history, which is why automakers like Stellantis (Chrysler/Fiat) and GM are partnering with Korean technology companies like LG Energy Solution and POSCO Future M. Innovative partnerships are also required on the design-build side to bring the right people to our project teams when delivering these facilities.
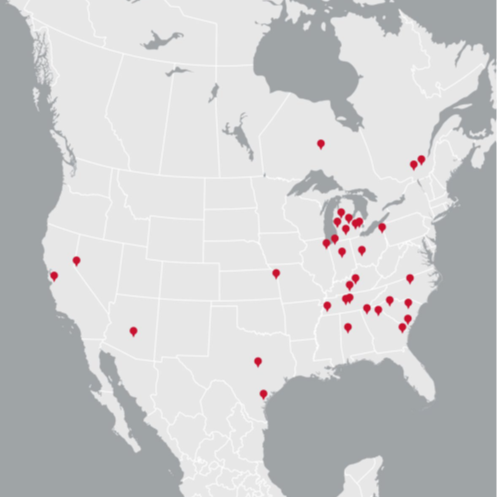
Locations of current North American EV megaprojects.
Rapid delivery
The North American EV market competes for expertise with phone and tablet manufacturers worldwide. It demands skilled labor specifically with “Advanced Manufacturing” experience, and it vies with virtually every industrial and commercial market for building infrastructure such as air-handling units, transformers and electrical switch gear. These facilities require three to four times the amount of mechanical and electrical systems of a typical manufacturing facility. Lead times can grow beyond 60 weeks to meet the massive demand of a single project. And any of these challenges can create delays.. Meanwhile, project delivery is no longer composed of rigidly delineated phases, which magnifies the need for ready solutions to the challenges above. Each phase overlaps the next. Funding continues even as schematic design commences and our construction team is assembled. Supplier selection takes place concurrent to design documents being formalized, which is concurrent to construction sequencing. When the facility roars to life and outputs its first products, our construction teams will still be on site to make any needed refinements. Never before have we seen this level of complexity in terms of concurrent design, procurement, fabrication and construction, where everything is happening at once.
Strategies for navigating dynamic interdependencies
Alberici builds facilities to serve each modality of the EV battery supply chain and has generated strategies for navigating the dynamic interdependencies. Our strategies have developed in a relatively short time through our focus on removing or mitigating uncertainties. These strategies have proven effective for projects such as NextStar Energy’s 4.5 million SF midstream facility and GM/POSCO Future M’s upstream facility.
Trade partner needs
Regional labor markets vary greatly. Self-perform capacity can remove labor uncertainty, especially when meeting aggressive schedules such as those at NextStar Energy’s plant in Windsor, Ontario. The project started in 2022, celebrated 30 percent completion in November 2023 and is expected to produce its first modules in the first half of 2024. To effectively divide project scopes, we qualified multiple subcontractors with the right experience and combined them with self-perform to meet the needs of this mega-project.
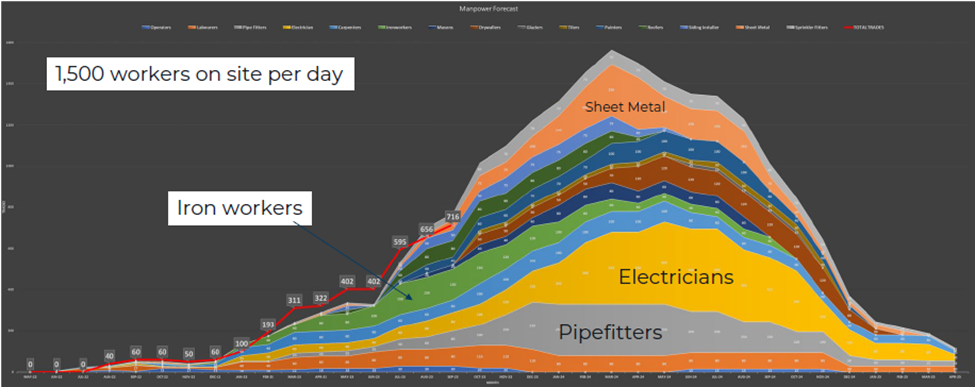
Figure above indicates fluctuations of specific trades as projects progress.
Scope alignment and change management
Given the size and diversity of our project teams, in terms of languages and standard operating procedures, communication channels need to be inclusive and established early on. Changes are almost a certainty as the project progresses and they can ripple in all directions from design and construction to procurement and funding. Alberici continually updates cost estimates as projects advance from phase to phase, and our estimates for specific scopes have at times changed by 20 percent or more because scope has grown or quantities have changed. We meticulously curate organizational charts separately for pre-construction and construction to rigorously define channels of information. In effect, we are generating scope alignment between all parties, ensuring clear communication of expectations.
Balancing risk and reward in contract
Ultimately, due to the size, scale, and “known unknowns,” the contract model used for these projects — between contractor and owner as well as contractor and subcontractor — has been widely variable. Whether influenced by cost, schedule, quality or management expertise, the contract is carefully considered to align desired outcomes among all parties. A lump-sum or fixed-price contract carries the greatest risk on the contractor side for scopes with the greatest uncertainty, but it can make sense for earthwork, architecture and landscaping scopes that are unlikely to change significantly. A Cost-Plus agreement carries less risk for the contractor and can make sense for scopes that anticipate limited change such as concrete and foundation work. A time and material (T&M) contract carries the lowest risk for MEP contractors, who agree to perform the scope of work, knowing that labor and material costs will change.
Moving forward
Even as EV sales have slowed recently, momentum continues to support a societal shift to reduce carbon emissions and embrace electric vehicles. Establishing a North American supply chain will continue to rely on specialized facilities regardless of political environment. Construction partners who understand and leverage these integrated supply chain tactics are a must to deliver these projects on time and with best value.
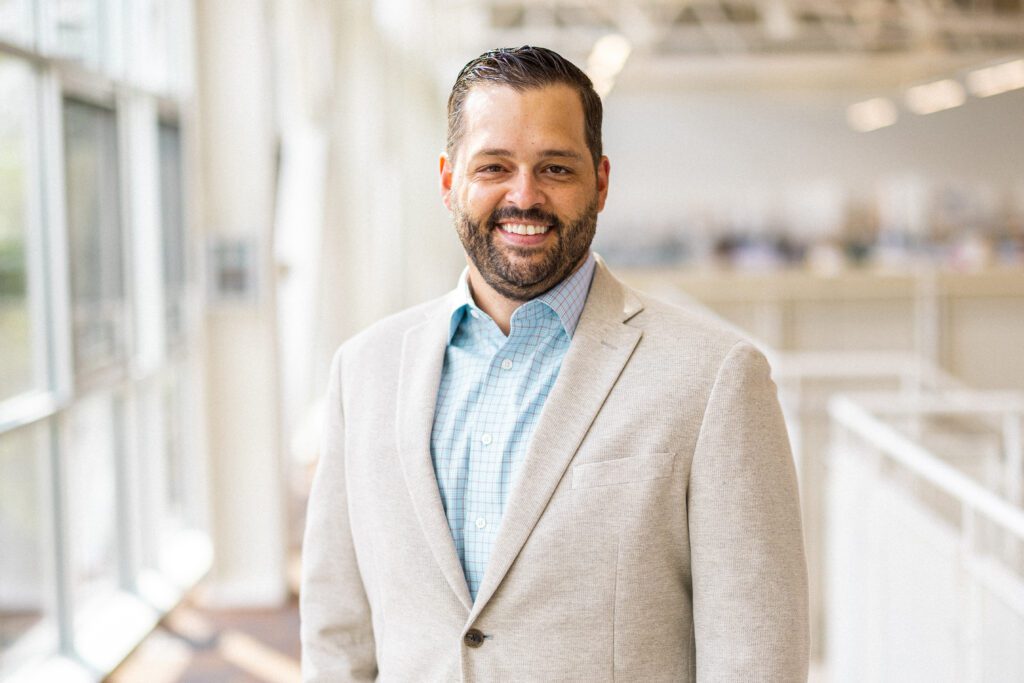
About Aaron Walsh – As Market Leader for Alberici’s automotive market based in Detroit, Aaron is responsible for overall operations, client satisfaction, and the financial success of his business unit. He drives strategy and builds relationships with clients and trade partners to lead successful pursuits.
Since joining Alberici 13 years ago, Aaron has steadily advanced through various roles including Project Manager and served as Director of Operations prior to assuming his current role. From equipment installation to new building construction and the emerging battery manufacturing market, Aaron has managed work across North America.