Successfully completing the largest hydroelectric plant on the Ohio River
Market
Energy & Renewables
Key Services
Construction
Self-Perform
Strategic Partnerships
Virtual Design & Construction
Self Perform %
79Capacity
105 MWWork Hours
2,450,000The challenge
Alberici led a joint venture team to construct the Meldahl Hydroelectric Plant. This project was part of a larger program to deploy the largest clean, renewable run-of-the river hydroelectric plant in the country. The powerhouse is designed to be overtopped during flood events by as much as 25 feet of water. During a period in the spring of 2015, construction continued inside the powerhouse while the entire powerhouse was submerged under 10 feet of water. Challenges included installation of a 175-ton powerhouse crane, which we later used to install the plant’s three bulb-type, 35 MW turbine generators. Our project team installed more than 5 million pounds of electrical and mechanical equipment, including massive water control structures with tolerances of a half-millimeter.
After construction of the structure was complete and the site was re-watered, Alberici coordinated a team of divers to perform inspections and perform hydraulic dredging of the intake structure at depths of up to 105 feet.
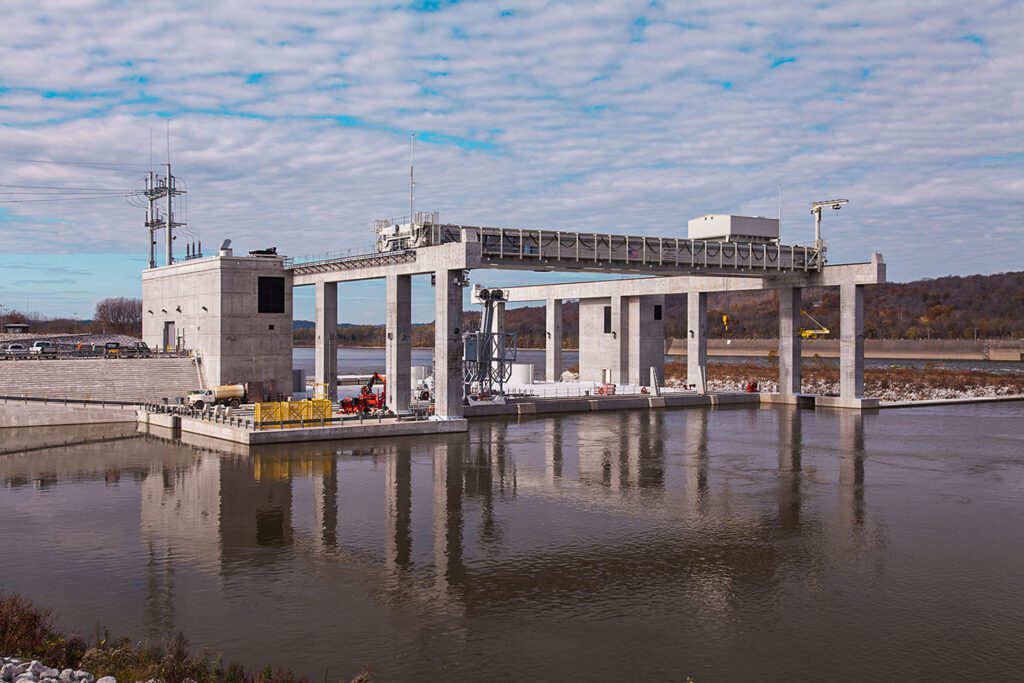
Key Facts
105 megawatts
Three horizontal bulb turbines
900 concrete placements
Challenge met
Alberici’s solution encompassed cutting-edge strategies and meticulous planning. A comprehensive 3D model and virtual schedule were developed to visualize construction sequencing within the powerhouse, enhancing accuracy and project insight. To manage groundwater seepage, an elaborate pump system was employed, discharging up to 5,500 gallons per minute around the clock to prevent flooding.
Emphasizing self-performance, Alberici’s skilled team undertook 79 percent of all work, including batch plant setup, concrete placement, steel erection, and equipment assembly. With innovative lift drawings, more than 900 individual concrete placements were precisely executed. An onsite batch plant facilitated seamless concrete production, ensuring quality and efficiency. Upon completion, the batch plant was transformed into a community recreation area.
Through strategic foresight, technical expertise, and collaborative coordination, Alberici navigated complexities to successfully deliver the hydroelectric plant. The project stands as a testament to Alberici’s commitment to innovation, precision, and excellence in challenging construction environments.